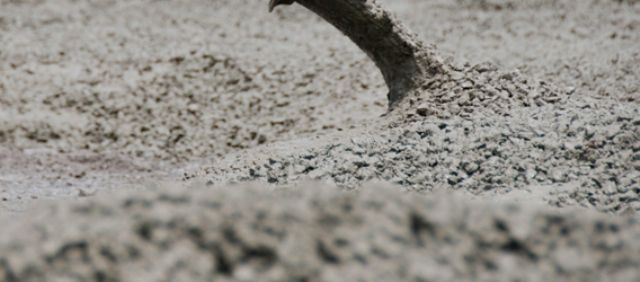
Fresh concrete, often known as plastic concrete, is a substance that has been recently mixed and may be moulded into any shape. Fresh concrete contains a variety of qualities that are necessary for constructing concrete structures on the job site. Fresh concrete’s most important qualities are addressed.
1. Workability
The phrase “workability” or “workable concrete” has a considerably broader and deeper meaning than the term “consistency,” which is sometimes used interchangeably with workability. Consistency is a broad concept that refers to the degree of fluidity or mobility. Concrete with high consistency and mobility does not have to be suitable workability for a certain job.
Concrete that is regarded workable for mass concrete foundations is not workable for roof building, and even when used in roof construction, concrete that is considered workable when vibrated is not workable when compacted by hand.
Similarly, concrete that is considered workable in thick parts is not workable when used in thin sections.
As a result, the term workability takes on the full meaning of the type of work, section thickness, reinforcing extent, and compaction mode.
To develop a mix, a concrete technologist needs a thorough understanding of workability.
Workability is a parameter that a mix designer must specify in the mix design process, along with a thorough grasp of the type of work, transport distance, slump loss, manner of placement, and many other variables.
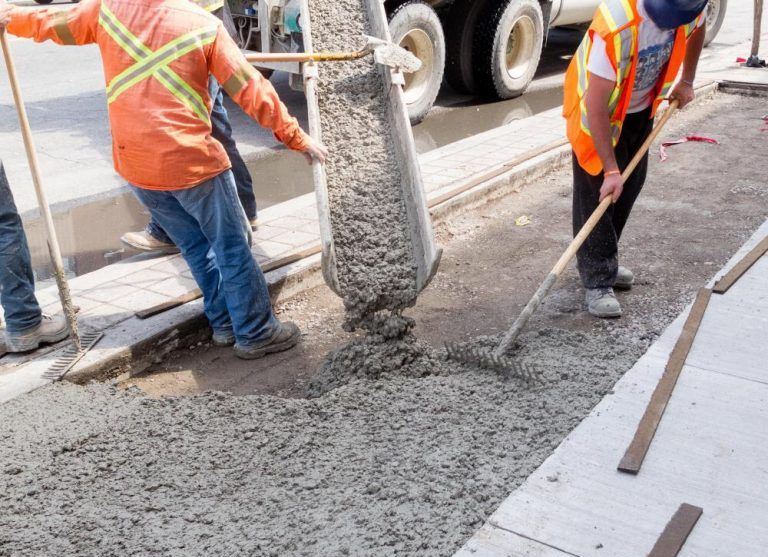
Factors affecting workability
Workable concrete is the one which exhibits very little internal friction between particle and particle or which overcomes the frictional resistance offered by the formwork surface or reinforcement contained in the concrete with just the amount of compacting efforts forthcoming.
The factors helping concrete to have a more lubricating effect to reduce internal friction to help easy compaction are given below:
- Water Content Mix Proportions
- Size of Aggregates Shape of Aggregates
- Surface Texture of Aggregate Grading of Aggregate
- Use of Admixtures.
2. Segregation
The separation of the constituent ingredients of concrete is referred to as segregation.
Good concrete is one in which all of the elements are evenly distributed to produce a homogenous mixture; if a sample of concrete shows a tendency for coarse aggregate to separate from the rest of the materials, that sample is said to demonstrate segregation. Such concrete would not only be weak, but it will also have all of the bad features of hardened concrete due to its lack of homogeneity.
There are three types of segregation:
- Coarse aggregate separating out or settling down from the rest of the matrix
- Paste or matrix separating away from coarse aggregate
- Coarse aggregate separating away from paste or matrix.
Reason for segregation
A poorly balanced mix in which there isn’t enough matrix to bind and contain the aggregates.
Concrete that has been improperly mixed and contains too much water has a higher tendency to segregate.
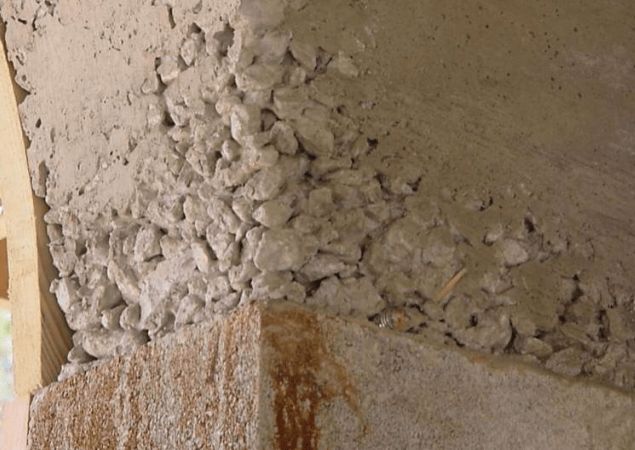
3. Bleeding
Water gain is a term used to describe bleeding.
It’s a type of segregation in which some of the water in the concrete escapes to the surface, owing to the fact that water has the lowest specific gravity of all the concrete elements.
Bleeding is most common in the extremely wet mix, poorly proportioned, and inadequately mixed concrete.
Excessive bleeding occurs in thin parts such as roof slabs or road slabs, as well as when concrete is put in bright weather.
Water rises to the surface as a result of the bleeding. Along with the water, a small amount of cement occasionally rises to the surface.
Bleeding water will most likely collect below the aggregate.
Water voids are created as a result of the buildup of water, which weakens the link between the aggregates and the paste.
In the case of flaky aggregate, the feature mentioned above is more evident.
Water that collects below the reinforcing bars, especially below the cranked bars, weakens the bond between the reinforcement and the concrete. Delay in finishing operations can reduce the production of laitance and the resulting negative effect.
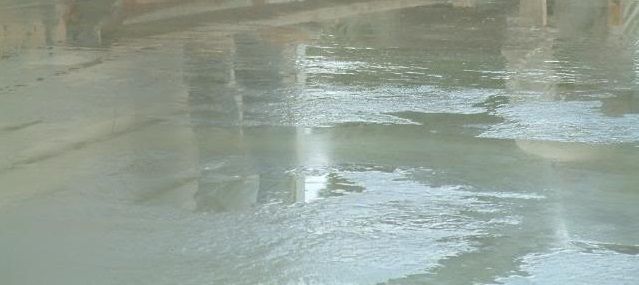
4. Setting Time of Concrete
Setting time of cement is found out by a standard Vicat apparatus in laboratory conditions. Setting time, both initial and final indicates the quality of cement.
