Hardware :
Components :
- Transformer 220:9 V. Diodes IN4007 X 2
- Electrolytic Capacitor 1000 Microfarad.
- I.C. 4N25 (Opto-Isolator)
- Resistor 1K.
- Transistor (BC148)
- Relay
- DB-25 male connector
Analog to Digital Converter: An A/D converter is used to convert analog signals to digital quantity. The digital output is fed to parallel port through multiplexer. The most popular method of analog to digital conversion is successive approximation method. This method has excellent compromise between accuracy and speed. We need not have to trade one thing for other. An unknown voltage Vin is compared with a fraction of reference voltage Vr. For n bits digital output comparison is made n times with different fractions of Vr and the value of a particular bit is set to 1, if Vin is greater than the set fraction of Vr. The bit is set to 0 if Vin is less than the set fraction of Vr.
Light Dependence Resistance: The resistance of LDR increases with decreasing intensity of incident light. When intensity of incident light decreases the voltage across LDR increases.
Rectifying Diodes (1N4007): These diodes have been used for rectification purposes. Rectification is the process of converting alternating signal into direct signal. It is generally complemented by a RC filter to clip off the ripples.
Small Signal Diode (1N4148): It is used for voltage regulation purposes. These diodes prevent circuit overloading. These also help in protecting the circuit from static charges.
3-Terminal Positive Voltage Regulator (LM7805): The 3-terminal positive voltage regulators employ built in current limiting, thermal shutdown and safe-operating area protection which make them virtually immune to damage from output overloads.
3.6.2 Relay :
The following circuit is the sample interface. You can use this to control relay from parallel port: Vcc
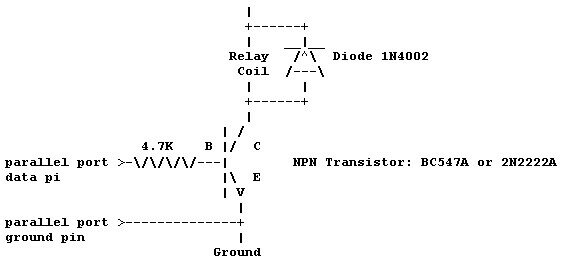
The circuit can handle relays which take currents up to 100 mA and operate at 24V or less. The circuit need external power supply which has the output voltage which is right for controlling the relay (5..24V depending on relay). The transistor does the switching of current and the diode prevent spikes from the relay coil form damaging your computer (if you leave the diode out, then the transistor and your computer can be damaged).
Since coils (solenoids and relay coils) have a large amount of inductance, when they are released (when the current is cut off) they generate a very large voltage spike. Most designs have a diode or crowbar circuit designed to block that voltage spike from hitting the rest of the circuit. If that diode is bad, then the voltage spike might be destroying your “sink” transistor or even your I/O card over a period of time. The mode of failure for the sink transistor might be short circuit, and consequently you would have the solenoid tap shorted to ground indefinitely.
The circuit can be also used for controlling other small loads like powerful LEDS, lamps and small DC motors. Keep in mind that those devices you plan to control directly from the transistor must take less than 100 mA current.
3.6.3 Opto isolator :
If you want to have a very good protection of the parallel port you might consider opto-isolation using the following type of circuit:

The opto-isolator is there to protect the port. Note that there are no connections between the port’s electrical contacts. The circuit is powered from external power supply which is not connected to PC if there is no need for that. This arrangement prevents any currents on the external circuits from damaging the parallel port.
The opto-isolator’s input is a light emitting diode.R1 is used to limit the current when the output from the port is on. That 1kohm resistor limits the current to around 3 mA, which is well sufficient for that output transistor driving.
The output side of the opto-isolator is just like a transistor, with the collector at the top of the circuit and the emitter at the bottom. When the output is turned on (by the input light from the internal LED in the opto-coupler), current flows through the resistor and into the transistor, turning it on. This allows current to flow into the relay.
Turning the input on the parallel port off causes the output of the opto-isolator to turn off, so no current flows through it into the transistor and the transistor turns off. When transistor is off no current flows into the relay, so it switches off. The diode provides an outlet for the energy stored in the coil, preventing the relay from back feeding the circuit in an undesired manner.
The circuit can be used for controlling output loads to maximum of around 100 mA (depends somewhat on components and operation voltage used). The external power supply can be in 5V to 24V range.
probably time to remove this article
as parallel ports are very rare
It will be good to provide the circuit diagram.
Some very fascinating factors however i think your analysis and bias leaves rather a lot to be desired. Then of course, that’s just my opinion. Have an amazing day undoubtedly a thought-frightening post.